Bio-fabrication of Artificial Blood Vessels with Laser Light
Thanks to the development of an artificial, three-layered perfused skin model, the EU research project ArtiVasc 3D is advancing into uncharted territories. An interdisciplinary team of researchers led by the Fraunhofer Institute for Laser Technology ILT has developed a 3D printing process for the production of artificial blood vessels out of innovative materials. They have created the foundation to cultivate a full-thickness skin model to a much greater layer thicknesses than previously possible. At the project’s closing event at Fraunhofer ILT from October 28 to 29, 2015, the ArtiVasc 3D researchers will present their findings in detail.
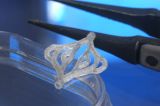
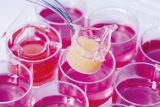
To date, it has only been possible to cultivate the upper layers of the skin – the epidermis and dermis – with a total thickness of up to 200 micrometers outside the human body. A complete skin system, however, also includes subcutaneous tissue having a thickness of several millimeters. If one wishes to co-cultivate the hypodermis, blood vessels supplying this tissue are imperative since, for cell aggregates of about 200 microns thickness, the following applies: no life without blood. This is where the European research project ArtiVasc 3D starts; it has set itself the goal of enabling significantly more complex tissues to be cultivated in vitro by developing artificial blood vessels.
The Right Material in the Right Form
One of the biggest challenges the project ArtiVasc 3D faced was to develop the right material for the production of artificial blood vessels. For them to be used in the human body, these vessels must have the correct mechanical properties and biocompatibility as well as full processability. Indeed, endothelial cells and pericytes must be able to colonize the artificial blood vessels.
In order to generate these properties, the Fraunhofer scientists combined the freeform methods of inkjet printing and stereolithography. With these combined processes, the researchers were able to achieve a very fine resolution for the construction of branched, porous blood vessels with layer thicknesses of about 20 microns. The researchers used mathematical simulations to develop data for the construction of branched structures. This data should create the conditions so that branched structures can be generated which allow uniform blood supply. The use of the acrylate-based synthetic polymer developed in the project permits the scientists to construct these optimized vessels with a pore diameter on the order of hundreds of microns. Compared to conventional methods, the ArtiVasc 3D process provides the general conditions to produce branched and biocompatible vessels in this size for the first time.
Foray into the Third Dimension
The results of ArtiVasc 3D are shaping the future. A toolbox has been developed that can respond flexibly to diverse materials, shapes and sizes. These results can be viewed as a precursor to a fully automated process chain for the production of artificial blood vessels, and which can also be integrated into existing lines. Another highlight of the project is the successful breeding of adipose tissue in a novel bioreactor. The combination of the fatty tissue with an existing skin model allowed the production of a full-thickness skin model which has a thickness of up to 12 millimeters.
The successful conquest of the third dimension need not be confined to the skin, however. The ArtiVasc 3D project has also laid the foundations for three-dimensional tissue engineering. By using the principle of blood circulation with artificial blood vessels, medical engineers will be able to build larger structures such as whole organs in the future. For full skin cultured in vitro, there are a variety of applications: quick assistance for large-area skin injuries such as burns or after tumor resection as well as a replacement model that would make animal testing in the pharmaceutical industry unnecessary.
Success Only in a Network
Not only should the blood vessels as such be developed, but also the technology that is required to cultivate the entire skin system fully automatically, within the four-year project period. This extremely ambitious challenge could only be achieved in an interdisciplinary network. All over Europe, twenty partners from the fields of biomaterial development, tissue engineering, freeform methods, automation and simulation have joined forces under the leadership of Fraunhofer ILT.
The ArtiVasc 3D Project Partners
- Aalto University
- Albert-Ludwig University of Freiburg
- AO Research Institute Davos
- International Management Services ARTTIC
- Beiersdorf AG
- Berufsgenossenschaftliche Kliniken Bergmannsheil [Bergmannsheil Hospital of the Ruhr-Universität Bochum]
- Fraunhofer Institute for Applied Polymer Research IAP
- Fraunhofer Institute for Interfacial Engineering and Biotechnology IGB
- Fraunhofer Institute for Laser Technology ILT
- Fraunhofer Institute for Production Technology and Automation IPA
- Fraunhofer Institute for Mechanics of Materials IWMINNOVENT e.V. Technology Development Jena
- KMS Automation GmbH
- Medical University of Vienna
- Unitechnologies SA
- University of East Anglia
- Loughborough University
- Institute for Interfacial Engineering and Plasma Technology IGVP, University of Stuttgart
- University of Salerno, Department of Industrial Engineering
- Vimecon GmbH
The research in the 3D ArtiVasc project has been financially supported in accordance with the grant agreement no. 263416 in the Seventh Framework Programme of the European Union (FP7 / 2007-2013).
Join our final workshop and learn more about the latest ArtiVasc 3D results!
On October 28 and 29, 2015, the ArtiVasc 3D researchers will be presenting their results in detail prior to the final workshop at Fraunhofer ILT in Aachen. We would be pleased to welcome you! Please fill in the registration form at www.artivasc.eu